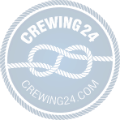
APRIL 12, 2013 — Mitsubishi Heavy Industries (MHI) has installed two EFD Induction "Terac 25" deck straightening systems at its main shipyard in Nagasaki, Japan. The Terac systems are currently being used to straighten decks and bulkheads on large cruise vessels.
Takehiko Nakagawa (left), Deputy Head, Cruise Ship Projects Department MHI, and Jan-Kåre Andersen, Product and Application Manager at EFD Induction, in front of the two Terac 25 systems
The Nagasaki shipyard is building two 3,250-passenger cruise ships for Carnival Corporation's AIDA Cruises.
"This is yet another high profile endorsement for the Terac," says Tetsuro Yanagawa, managing director of EFD Induction Japan. 'MHI are known worldwide for their shipbuilding expertise and efficiency, so their choice of Terac is a real sign of approval.'
Each of the two Terac 25s delivered to MHI is a turnkey solution that is housed in a standard 1.8m (5' 9") container.
"A small footprint is essential in busy shipyards," says Mr. Yanagawa. 'But despite its compact size, the Terac has been documented to cut straightening times by as much as 80 per cent compared to flame heating and other traditional methods."
Straightening ship decks and bulkheads with open flames is slow, expensive and potentially dangerous. Induction straightening, however, is fast, easy and safe. The process works by inducing eddy currents in the steel plate. This causes extremely rapid through-heating in a very concentrated area, which in turn expands vertically. As the heat affected zone cools, the surrounding material shrinks equally in all directions, permanently shortening and straightening the plate.
"The through heating achieved by induction," adds Mr. Yanagawa, "means only one side of a deck or bulkhead needs to be heated. With flame straightening, an operator typically has to heat both sides. Also, with a Terac the temperature and time parameters are set in advance, so it virtually impossible to overheat the metal."
The Teracs were delivered to MHI's Nagasaki yard several months ago, and have been working according to specifications.
"A key benefit of the Terac," says EFD Induction product manager Jan-Kåre Andersen, "is its ease of use. It takes years to train a skilled flame operator. But it takes only a few hours to learn how to correctly use a Terac. It's a straightening process that takes shipbuilding efficiency to another level."